Легированная сталь – это сплав железа с углеродом, в который входят дополнительные легирующие добавки (хром, марганец, никель, вольфрам, ванадий, ниобий, титан). Они придают стали улучшенные характеристики – коррозионная стойкость, повышенная прочность и жаростойкость.
Нержавеющие, инструментальные и быстрорежущие стали – виды легированной стали, широко использующиеся в промышленности.
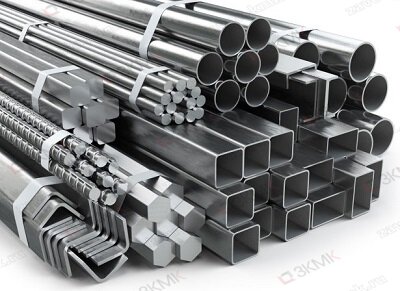
Чтобы сплав железа и углерода назывался сталью, в нём должно быть не менее 45 % железа, и содержание углерода в диапазоне от 0,02 до 2,14%.
По содержанию легирующих добавок легированные стали делятся на:
- низколегированные — до 4% легирующих элементов,
- среднелегированные — до 11% легирующих элементов,
- высоколегированные — свыше 11% легирующих элементов.
По назначению легированные стали делят на:
- Конструкционная сталь – применяется для производства строительных конструкций и высоконагруженных механизмов. Легируются хромом (от 0.8% до 1.2%), а также бором, никелем, молибденом, марганцем, кобальтом, титаном
- Инструментальная сталь – для изготовления режущих, штамповочных или измерительных инструментов. Легируются большим количеством хрома (его содержание может достигать 12%), ванадием, титаном, вольфрамом, марганцем
- сталь с особыми физическими или химическими свойствами – нержавеющая, жаропрочная (содержат до 25% хрома и 20% никеля), износостойкая (содержат углерод, хром и молибден), магнитная, немагнитная, с высоким электросопротивлением – или стали специального назначения – шарикоподшипниковые, шарнирно-рессорные, пружинные, быстрорежущие, криогенные, авиационные.
Существует много высоколегированных сплавов специального назначения. Например, сталь 15Х2НМФА разработана для корпусов и крышек реакторов, а из сплава AISI 316L (с молибденом и никелем) изготавливают медицинские имплантаты.
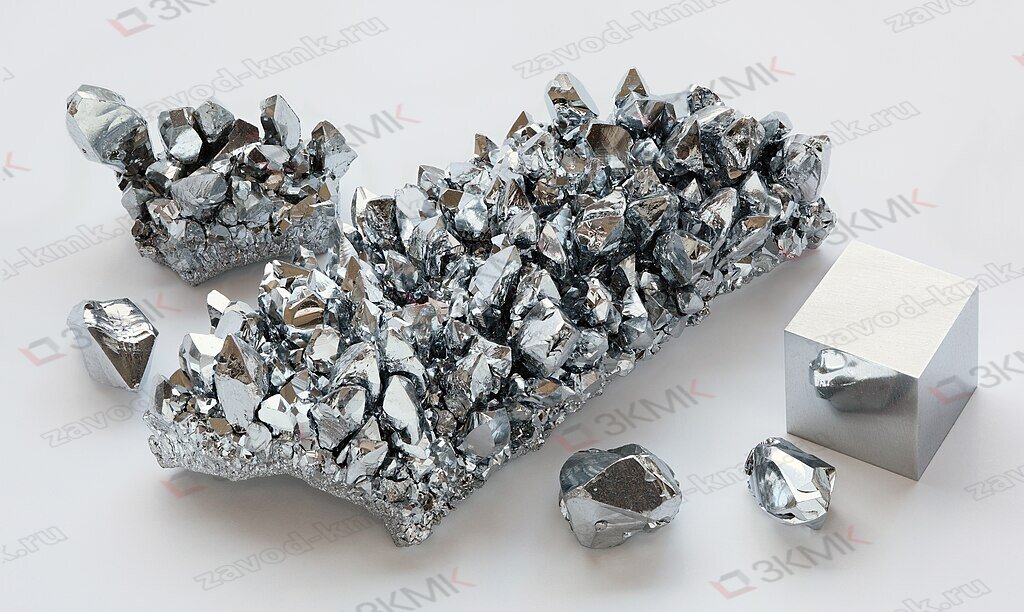
В России и странах СНГ принято буквенно-цифровое обозначение качественных углеродистых и легированных сталей, указывающее на их химический состав, степень очистки и специальное назначение.
Две первые цифры показывают содержание углерода в сотых долях процента, цифры после буквы – содержание соответствующего элемента в процентах. Если цифры не указаны, то легирующего элемента содержится 0,8—1,5 % (кроме молибдена, ванадия и бора). Например, 12Х18Н10Т – нержавеющая легированная сталь с содержанием углерода не больше 0,12 %, а хрома, никеля и титана – не более 18, 10 и 1 процента соответственно.
Отдельные группы сталей маркируются иначе:
- быстрорежущие стали маркируются начиная с буквы Р, после которой указывается количество вольфрама в процентах. Например, Р17 – быстрорежущий сплав, содержащий 17% вольфрама
- шарикоподшипниковые стали маркируют буквами ШХ, после которых указывают содержания хрома в десятых долях процента, например, ШХ 15
- автоматные стали обозначают буквой А и следующей цифрой указывают содержание углерода в десятых долях процента.
Маркировка легированных сталей регулируется ГОСТ 4543-2016.
Для стали в Европе и Америке используется система маркировки AISI. Углеродистые и легированные стали по этой системе обозначаются четырьмя цифрами, иногда с буквами, например, 1045. Углеродистым сталям соответствуют маркировки 10XX, 11XX, 12XX и 15XX. Остальные чётырёхбуквенные обозначения указывают на легированную сталь.
Нержавеющие (коррозионностойкие) легированные стали по AISI маркируются тремя цифрами, после которых могут следовать буквы. Например:
- сталь 304 – сталь аустенитного класса с содержанием углерода < 0.08%,
- сталь 304 L – сталь аустенитного класса с пониженным содержанием углерода, < 0.03%,
- сталь 304 N – легированная азотом сталь 304,
- сталь 430 F – мартенситно-ферритная сталь с повышенным содержанием серы и фосфора.
Для легированных сталей используется также европейская система EN, схожая с российской буквенно-цифровой. Так, X5CrNi18-10 (1.4301) обозначает нержавеющую аустенитную сталь, где X указывает на сплав, 5 на содержание углерода в сотых долях процента (0.05% углерода), CrNi на присутствие хрома и никеля, а 18-10 на их содержание (около 18% хрома и 10% никеля).
По структуре легированные стали делятся на ферритные, перлитные, аустенитные, мартенситные, ферритно-мартенситные и другие. Эта классификация основана на том, какие кристаллические структуры присутствуют в стали после охлаждения до комнатной температуры и при нормальном давлении.
Существует пять основных типов структуры стали: ферритная, аустенитная, перлитная, мартенситная и карбидная.
- В ферритной стали преобладает феррит – кристаллическая структура железа с низкой твёрдостью и прочностью. Ферриты магнитны и имеют неустойчивую кристаллическую решётку. Ферритные стали – это низколегированные и углеродистые.
- Аустенитные стали. Кристаллическая структура аустенита образуется при нагреве стали до высокой температуры. Аустенитные стали содержат никель, хром и марганец и наибольшее количество легирующих элементов среди всех легирующих сталей. Жаро- и хемостойки, пластичны, не боятся коррозии. В эту группу входят хромоникелевые нержавеющие стали.
- Перлитная сталь содержит перлит – смесь феррита и цементита (карбида железа). Имеет среднюю прочность и твёрдость, используется как конструкционная сталь.
- Мартенситная сталь образуется при быстрой закалке перлитной стали. Мартенсит хрупкий, твёрдый и прочный, плохо обрабатывается и имеет магнитные качества.
- Карбидная сталь содержит карбиды – соединения углерода с различными металлами, в первую очередь цементит. Стали этого класса имеют высокую твёрдость, износостойкость, теплостойкость и обычно используются для изготовления ножей.
Структура стали влияет на способы её обработки и механические свойства.
В зависимости от того, как легирующий элемент взаимодействует с углеродом или железом, он по-разному влияет на свойства стали. Основные свойства легированных сталей:
- Повышенная прочность без термической обработки за счёт упрочнения феррита после растворения в нём легирующих элементов.
- Повышение твёрдости, прочности и ударной вязкости за счёт увеличения устойчивости аустенита и прокаливаемости. Ударная вязкость при растворении легирующих элементов в феррите может снижаться.
- Многие легирующие элементы придают стали жаропрочность и коррозионную стойкость.
Основное преимущество легированных сталей по сравнению с углеродистыми – возможность варьировать эксплуатационные характеристики, добавляя в сплав элементы, придающие ему требуемые свойства. Однако легированные стали имеют и недостатки, например:
- Высокая стоимость материала за счёт дорогих легирующих добавок.
- Сложность технологического процесса и обработки стали зависит от используемых добавок. Неправильный выбор или использование легирующих элементов приводит к непредсказуемым эффектам.
- Легированная сталь сложнее в обработке, в том числе термо-. Сварка легированной стали требует специального оборудования и подготовки либо вовсе невозможна (для никелевых сплавов).
- Обратимая отпускная хрупкость у марганцевых, хромистых, хромоникелевых легированных сталей, вызывающая снижение их ударной вязкости после отпуска и охлаждения.
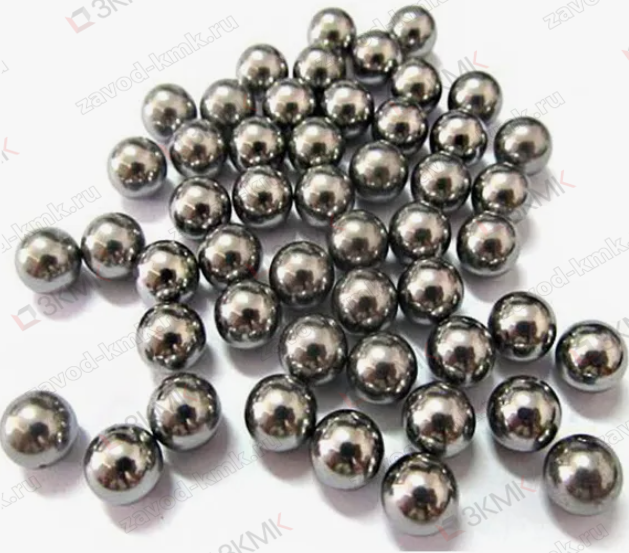
В металлургическом производстве применяются два основных метода легирования: объёмное, или металлургическое, и поверхностное.
Объёмное легирование производится введением в весь объём расплава дополнительных веществ, улучшающих его свойства. Ведётся в тигельных, индукционных, дуговых, плазменных и других печах.
При способе объёмного легирования теряются большие количества дорогостоящих добавок – хрома, молибдена, титана. Для уменьшения потерь используют лигатуры и ферросплавы – вспомогательные сплавы из двух и более компонентов, предназначенные для введения в расплав тугоплавких материалов. В никелевых сплавах в качестве лигатур применяются алюминий, марганец, цирконий или цинк. Ферросплавов существует множество – феррохром, ферросилиций, ферровольфрам и другие.
Комбинация термической обработки и пластической деформации называется термомеханическим легированием и особенно эффективна для микролегирования, при котором в состав вводятся крайне малые доли легирующих элементов (менее 0,1 %).
Поверхностное легирование применяют для изменения приповерхностного слоя сплава (от нескольких микрометров до 1-2 мм). Выполняется множеством способов: диффузионным насыщением из газовой или жидкой фазы, химическим осаждением из газовой фазы, твердофазным методом (нанесение на поверхность легирующих элементов с последующим оплавлением).
Поверхностным легированием можно назвать и цинкование – нанесение на поверхность металла защитного слоя цинка холодным или горячим способом.
Лазерное легирование – современный метод легирования, при котором легирующие элементы вносятся в поверхностный слой стали, а затем расплавляются лазерным или электронным пучком. Метод используется при изготовлении режущих инструментов и деталей, работающих под высокой нагрузкой.
Легирующие добавки делятся на металлические и неметаллические. В маркировке стали по ГОСТ традиционно обозначаются кириллицей.
Легирующие металлы:
- хром, Х – увеличивает твёрдость и коррозионную стойкость. Основной легирующий компонент нержавеющей легированной стали
- никель, Н – увеличивает теплоёмкость, вязкость, пластичность и снижает хрупкость, что облегчает обработку стали
- вольфрам, В и молибден, М – увеличивают прочность при термической обработке и коррозионную стойкость
- марганец, Г – снижает отрицательное влияние серы, фосфора и кислорода
- медь, Д – повышает прочность легированной стали и снижает уровень вязкости. Используется для изготовления строительной стали
- ниобий, Б – увеличивает стойкость к химической коррозии
- кобальт, К – увеличивает жаропрочность и ударную вязкость
- титан, Т и цирконий, Ц – уменьшают уровень зернистости и придают сплаву однородную структуру
- ванадий, Ф – улучшает структуру сплава и увеличивает жаропрочность
- алюминий, Ю – предотвращает появление окалины и уменьшает количество остаточных аустенитных зёрен после термообработки.
Также в легированные стали добавляют неметаллические элементы:
- селен – увеличивает текучесть и обрабатываемость механическим способом
- бор – улучшает структуру сплава и его прокаливаемость
- азот – улучшает механические свойства стали. Азот добавляют в высоколегированные стали.
Легирующие добавки по-разному влияют на свойства стали. В зависимости от добавленных элементов, различают хромомарганцевокремниевые легированные стали (30ХГС, ЗОХГСА, и подобные), хромоникелевые (12ХН3А, 20ХН, 30ХН), хромоникельмолибденовые (30Х2Н2МА и подобные), сильхромы (33ХС, 38ХС) и другие.
Кроме того, в состав стали всегда входят примеси, которые попадают в неё из чугуна, как раскислители или во время выплавки – сера, фосфор, кислород, марганец, кремний, азот. Из руды в сталь попадают медь, мышьяк, свинец, олово, цинк. Их влияние на сплав не всегда положительно, и его стараются минимизировать.
Из-за высокой прочности и коррозионной стойкости легированная сталь применяется во многих областях промышленности:
- в автомобилестроении, машиностроении и энергетике, для создания прочных и износостойких деталей
- в строительстве, для высоконагруженных, долговечных и устойчивых к коррозии конструкций
- в химической и нефтегазовой промышленности, для изготовления устойчивых к эксплуатационным условиям деталей и механизмов
- в инструментостроении, для производства режущих, штамповочных и измерительных инструментов
- в медицинской промышленности, для производства хирургических инструментов, имплантатов и протезов
- в производстве бытовой техники и электроники
- в лёгкой промышленности, для изготовления товаров бытового назначения, в том числе нержавеющей посуды
- в производстве кабельных лотков металлических, крышек для металлического лотка, кабель каналов стальных оцинкованных, стоек и полок кабельных ГЭМ, где особенно важны антикоррозионные и прочностные характеристики стали.
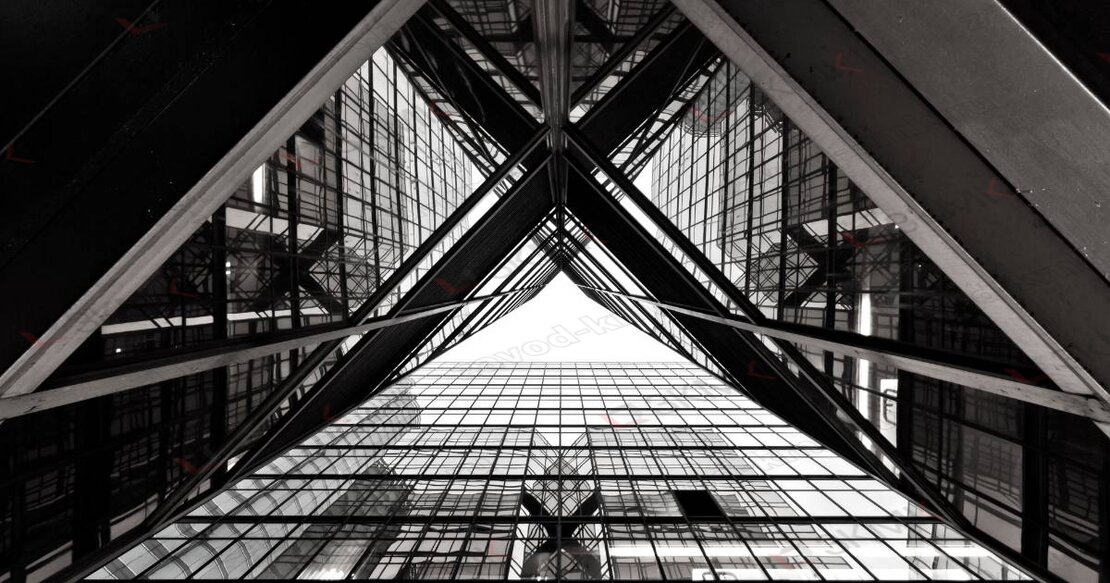
Углеродистые стали – это класс сплавов с повышенным содержанием углерода (до 2,14 %), наличием в составе кремния, марганца, серы и фосфора и отсутствием иных легирующих добавок. Такие сплавы отличаются хорошей прочностью и обрабатываемостью, но уязвимы к коррозии. Из углеродистой стали делают инструменты для металло- и деревообработки, а также инженерные и строительные конструкции.
Нержавеющая сталь – это особый класс легированных сталей, содержащих 12—20 % хрома и 8-10 % никеля, что придаёт сплаву повышенную коррозионную устойчивость по сравнению с другими легированными составами. В нержавейках используются и другие легирующие добавки. Например, фосфор и медь существенно повышают стойкость стали против атмосферной коррозии, а молибден – стойкость к хлоридам.
Под обычной сталью, как правило, понимается углеродистая сталь. По сравнению с легированной сталью, в ней отсутствуют легирующие элементы, но есть постоянные примеси. Поэтому свойства этих двух типов сталей существенно различны.
Также под обычной сталью иногда понимается углеродистая сталь обыкновенного качества – это строительная сталь Ст, содержащая углерод в количестве меньше 0,6%. Строительная сталь дешева и хорошо сваривается, но уступает другим сплавам по прочностным характеристикам и устойчивости к коррозии.
Узнать, что сталь легированная, можно следующими способами:
- По маркировке. Легированные стали маркируются буквенно-цифровым обозначением, где буквы указывают на легирующую добавку, а цифры – на её содержание. Состав стали, маркированной по системе AISI, можно определить по справочнику марок.
- Искровым методом. Опытные металлурги определяют марку стали по цвету и количеству искр при контакте стали с наждачным кругом. Так, например, хромистая сталь даёт бледно-жёлтые прерывистые искры с крупными редкими звёздочками.
- По цвету. Легированная сталь обычно имеет матовый более светлый оттенок, а поверхность нержавейки по сравнению с ней сильнее блестит и отражает свет.
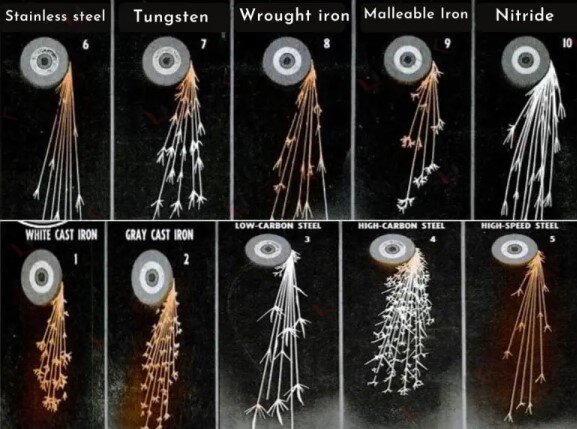
Иногда под видом легированной стали продаётся чёрный металл, покрытый хромом – это подделка. Она обладает привлекательным внешним видом, но не имеет коррозионной стойкости. Отличить качественную легированную сталь от подделки можно по цене или сдав материал на химический анализ.
Легированная сталь, в отличие от нержавеющей, не имеет защитного слоя оксидов хрома. Поэтому она может ржаветь.
Насколько сильно подвержена коррозии легированная сталь, зависит от состава и количества введённых в неё легирующих элементов. Чтобы защитить сталь от коррозии, рекомендуется цинкование, покраска или порошковое покрытие.
Добавить комментарий