Что такое порошковая покраска
Порошковая покраска – это метод окрашивания детали лакокрасочным покрытием с последующей термической обработкой, альтернатива традиционному нанесению жидкой краски.
Метод порошкового окрашивания – нанесение жидкого покрытия с порошкообразными добавками на основе модифицированных полимеров. Частицы порошка удерживаются на поверхности детали электростатическим притяжением. При температуре около 200°С нанесённое покрытие расплавляется и полимеризуется в равномерный прочный слой – устойчивый к царапинам и сколам, с высокими декоративными свойствами.
Порошковым методом окрашиваются металлические изделия, которые выдерживают нагрев до 200 °C (нержавейка, никель, медь, титан, латунь), керамика и стеновые изделия, древесноволокнистые плиты МДФ и стекло. Окраска при помощи порошка используется в отраслях:
- автомобиле-, мото- и судостроение – для покраски кузовов, корпусов, колёсных дисков;
- строительство – для защиты от коррозии и придания декоративного вида металлоконструкциям – ограждениям, решёткам, рольставням, дверям, для окрашивания инженерных коммуникаций, кабельных металлических лотков, полок кабельных, коробов кабельных металлических;
- мебельное производство – окрашивание мебели для эксплуатации на открытом воздухе;
- производство метизов и металлоизделий – для окраски винтов, саморезов, заклёпок;
- производство бытовой техники – окраска стиральных и посудомоечных машин, газовых и электрических печей, плит, вытяжек и сушилок белья;
- производство промышленного оборудования, станков, инструмента.
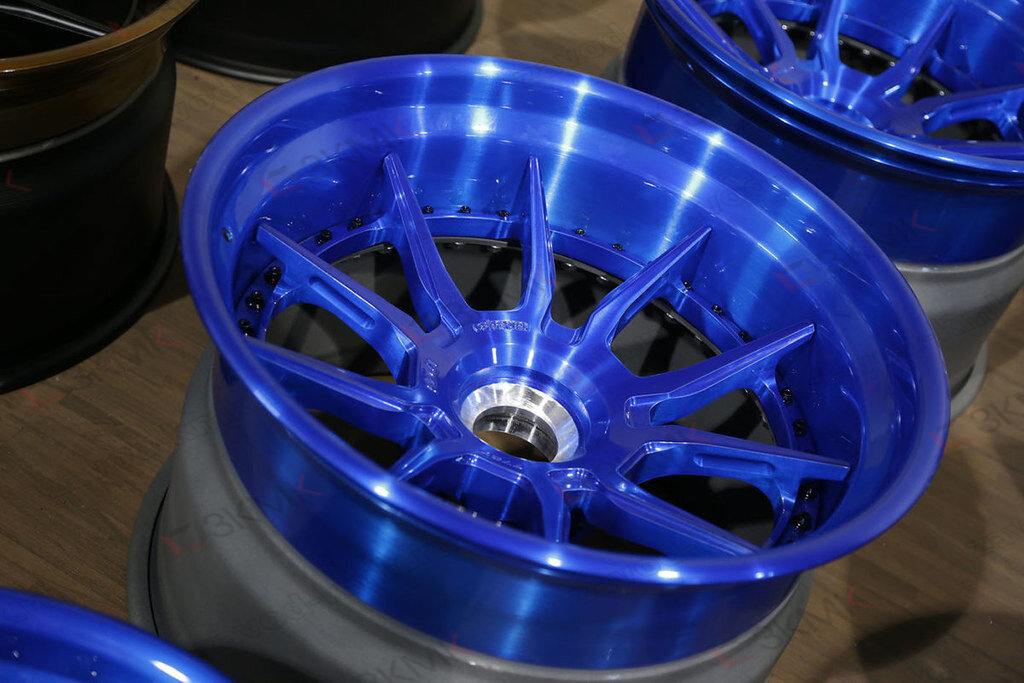
Существуют четыре основных способа порошковой окраски.
При помощи пистолета со сжатым воздухом, который на выходе из ствола заряжает частицы краски (отрицательным зарядом). Далее частицы краски притягиваются к заземлённой детали. Окрашенная поверхность помещается в печь или камеру полимеризации, где краска окончательно затвердевает при высокой температуре.
Электростатический способ создаёт плотное лакокрасочное покрытие, часто используется для нанесения красок металлик.
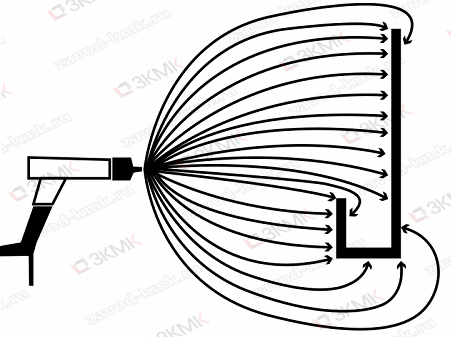
Как и в электростатическом способе, покраска происходит пистолетом со сжатым воздухом, однако частицы краски получают заряд, двигаясь по абразивному покрытию внутри ствола пистолета.
Трибостатический способ дает тонкое устойчивое покрытие, но процесс медленный и подходит не для всех красок.
Газопламенное напыление – самый доступный способ, не требующий использования печей или камер полимеризации. Высокотемпературный поток создаётся газовой горелкой (с ацетиленом, кислородом, пропаном, метаном). Термопластичный порошок, попадая в пламя, плавится и покрывает изделие.
Минусы метода – высокая пористость покрытий и большие тепловые потери.
При окраске способом флюидизированного нанесения заземлённая деталь вращается в облаке заряженных аэрозольных частиц порошка. Образуется плотное, равномерное и прочное покрытие. Годится для термопластичных и термореактивных порошков. Требует обязательного нагрева детали перед обработкой.
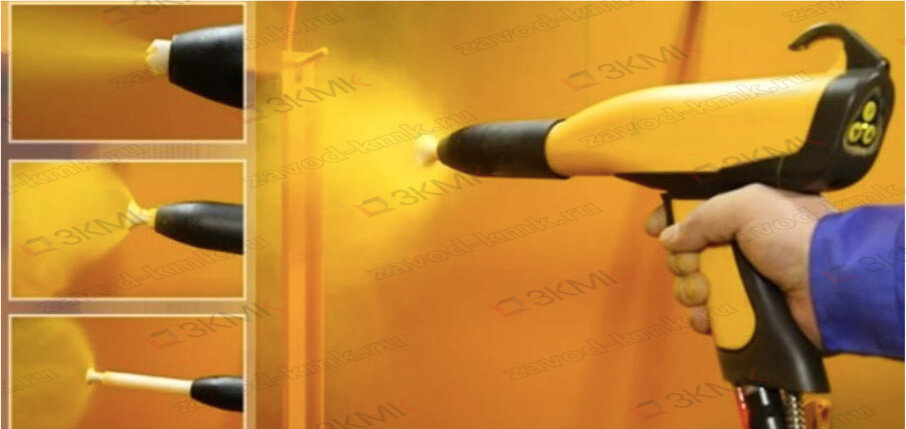
Основных этапов метода – пять штук:
- Подготовка поверхности – обезжиривание, удаление окисных плёнок, нанесение конверсионного покрытия (фосфатизация или хроматизация для улучшения сцепления краски с поверхностью). Для очистки загрязнений используется очистка паром, погружная или высокого давления мойка, пескоструй.
- Грунтовка, при необходимости. Грунтовка обеспечивает гладкое основание для финишного слоя и предохраняет материал от коррозии.
- Нанесение окрашивающего слоя по выбранной технологии.
- Отверждение лакокрасочного покрытия в полимеризационной печи, если требует технология покраски. Происходит при температурах 160…230°C, длительность зависит от размера и формы детали (как правило, 10-40 минут).
- Окончательное формирование покрытия во время остывания изделия.
Оборудование для окраски зависит от метода и включает:
- пистолет-распылитель для нанесения краски;
- покрасочную камеру, оснащённую вентиляцией и системой рекуперации – улавливания и возврата распылённых частиц;
- питатель – подаёт лакокрасочный материал в распылитель, вибросито – просеивает краску из системы рекуперации;
- компрессор для сжатого воздуха;
- полимеризационную печь, размеры и конструкция зависят от окрашиваемых деталей;
- транспортная система для перемещения деталей по производству;
- адгезиметр, толщиномер, термограф – приборы контроля качества покрытия.
Порошковые краски – однородный, физически и химически стабильный состав с диаметром частиц 50-100 мкм, который содержит твёрдые частицы, плёнкообразующие смолы, отвердители, наполнители.
Типы порошковых красок по классу основы, которая обеспечивает затвердевание:
- Термопластичные композиции. На основе винила, нейлона, полиэстера. Частицы термопластичных композиций сплавляются между собой только за счёт высокого давления и высокой температуры. Требуют предварительной грунтовки.
- Термореактивные. В состав входит катализатор, который после нагревания запускает химическую реакцию, образующую на поверхности детали прочную плёнку. Термореактивное покрытие невозможно растворить повторным нагреванием.
- На ультрафиолетовой основе. Отверждение композиций происходит при попадании на краску УФ-лучей.
Категории термореактивных красок – в зависимости от состава смол:
- Эпоксидные. Очень прочные, устойчивые к воздействию агрессивных веществ – химикатов, масел, топлива. Не требуют предварительного грунтования, могут сами использоваться как грунтовка. Не проводят электричество, поэтому применяются при окраске радио- и электротехнических элементов.
- Эпоксидно-полиэфирные. Обладают наименьшей устойчивостью к внешнему воздействию, но высокой декоративностью – эпоксидно-полиэфирные смолы придают материалу вид старой кожи или патины.
- Полиэфирные. Высокоадгезивные, применяются при покраске металлов. Устойчивы к атмосферным и механическим воздействиям, не проводят электричество, чувствительны к действию щёлочи.
- Уретановые. Сходны по свойствам с полиэфирными, используют для отверждения другие инициаторы, стоят дороже.
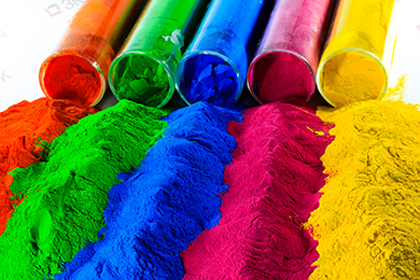
- Покрытие, стойкое к коррозии, механическим повреждениям, воздействию окружающей среды, высоких и низких температур и агрессивных сред. Срок службы – более 15 лет.
- Низкий расход краски по сравнению с традиционными методами распыления и, как следствие, минимизация расходов.
- Отсутствие дефектов (неровности, потёки), возникающих при нанесении жидких ЛКМ.
- Отсутствие растворителей снижает пористость покрытия и его усадку.
- Окраска деталей любой формы и конфигурации.
- Высокая скорость нанесения покрытия.
- Производство автоматизировано и не требует высокой квалификации персонала.
- Меньшая степень взрыво- и пожароопасности по сравнению с жидкой покраской.
- Декоративные качества покрытия, возможность создавать специальные эффекты (металлик, муар, старение, имитация дерева или кожи).
- Высокая температура плавления порошка – около 200°С, что исключает работу с пластиком и деревом.
- Запуск линии порошковой покраски требует дорогостоящего оборудования, в том числе специализированных печей и системы вентиляции.
- Есть ограничения по габаритам деталей – маленькие детали невыгодно красить в большой печи, а в маленькую печь не помещаются большие детали.
- Невозможно окрашивание в холоде – помещение с установкой должно быть хорошо отапливаемым.
- Невозможно нанести краску тонким слоем.
- Невозможно перекрасить отдельный участок изделия, для устранения локальных дефектов перекрашивают деталь целиком.
- Для колеровки порошковой краски используется международная палитра RAL. Колеровать краску в произвольный цвет нельзя, смешивание красок разных оттенков не допускается.

Срок службы порошковой краски зависит от условий эксплуатации и вида металла. В среднем покрытие держится 15-20 лет.
Устойчивость покрытия к высоким и низким температурам зависит от вида краски и метода её нанесения. Как правило, окрашенные детали выдерживают температуру от –60 до +150 °С.
Подготовка металла к порошковой покраске – обезжиривание, очистка или промывка чистящими средствами. Если поверхность сильно повреждена ржавчиной или оксидной плёнкой, проводится ручная, механическая или пескоструйная очистка налёта.
Также используется химическое травление и пассивация фосфатированием или хроматированием.
Давление воздуха на распылителе при порошковой окраске небольшое и составляет около 0,8 – 1,5 МПа. Существуют нормы, которым должен соответствовать сжатый воздух:
- содержание масла – менее 0,01 мг/м³,
- содержание влаги – менее 1,3 г/м³,
- содержание точек росы – менее 7°C,
- содержание пыли – менее 1 мг/м³.
Добавить комментарий